Capacity is the maximum level of output that a company can sustain to make a product or provide a service Planning for capacity requires management to accept limitations on the production Level Loading is a method that refers to maintaining a constant repetitive rate and load across your resources This method is often used when demand peaks in business outstrip available capacityRole of Aggregate Planning in a Supply Chain Basic Assumptions – Capacity has a cost – Lead times are greater than zero Aggregate planning – Is the process by which a company determines levels of capacity, production, subcontracting, inventory, stockouts, and pricing over a specified time horizon – goal is to maximize profit Or, if demand is effectively fixed for all the decision we
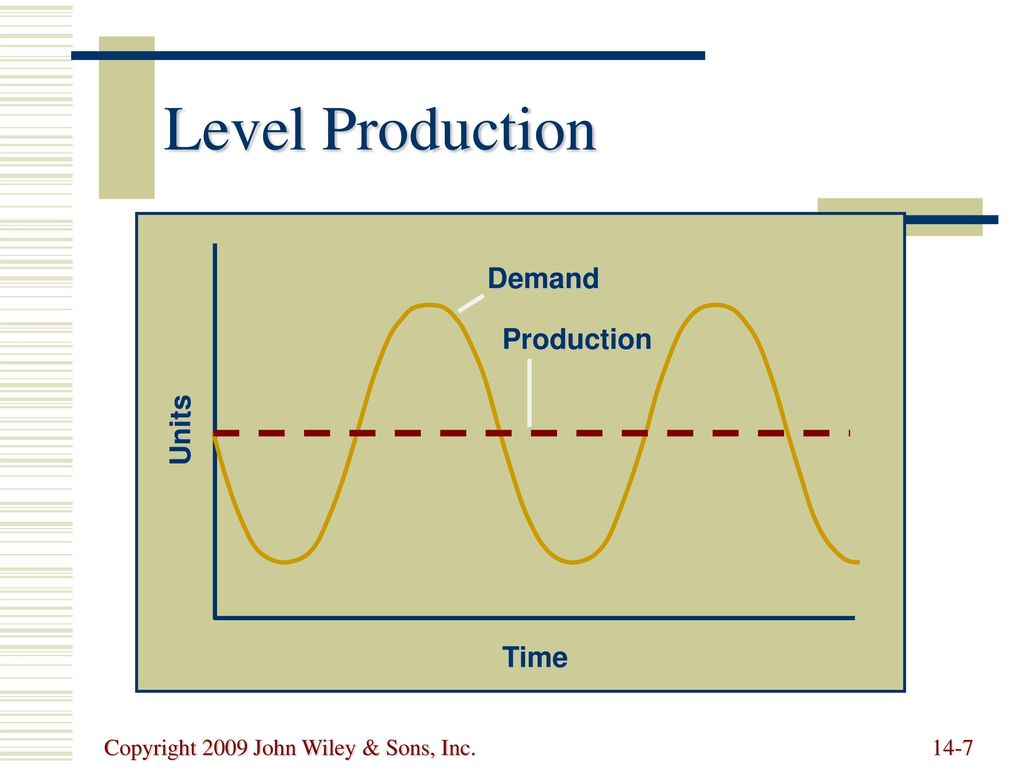
Sales And Operations Planning Ppt Download
Level capacity plan maintains production activity at a constant rate
Level capacity plan maintains production activity at a constant rate- Monetary policy has lived under many guises But however it may appear, it generally boils down to adjusting the supply of money in the economy to achieve some combination of inflation and output stabilization Most economists would agree that in the long run, output—usually measured by gross domestic product (GDP)—is fixed, so any changes in the money supplyManager A is in charge of the cashiering operation—the
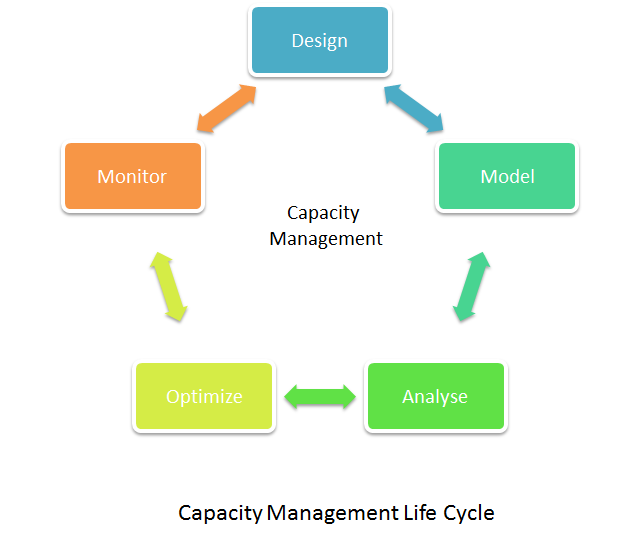



What Is Capacity Management Definition And Faqs Omnisci
Implement preemptive, corrective actions; We use your LinkedIn profile and activity data to personalize ads and to show you more relevant ads You can change your ad preferences anytime Monitor this counter to make sure that you maintain a level of at least percent of the total available physical RAM Memory Pages/sec This counter shows the rate at which pages are read from or written to disk to resolve hard page faults Monitor this counter to make sure that it remains under 100
Ensure upgrades are budgeted in a timely fashion;Or (3) working at a production rate pace while constantly pushing or pulling materials even though the weight of the materials is negligible (The constant stress and strain of maintaining a production rate pace, especially in an industrial setting, can be and is physically demanding of aThe cash flows are expected to grow at a constant rate after year 3, forever If the initial investment is $ 1 million and the cost of capital is 12%, how high would the growth rate have to be after year 3 to justify taking this project?
Electricity generation In , net generation of electricity from utilityscale generators in the United States was about 4,009 billion kilowatthours (kWh) (or about 4 trillion kWh) EIA estimates that an additional 417 billion kWh (or about 004 trillion kWh) were generated with smallscale solar photovoltaic (PV) systemsAchieving and maintaining quality performance is important to the target population, to funders, and to the community Using some TQM principles and, specifically, the Deming Cycle (Plan, Do, Check, Act, Analyze) can be helpful in getting to a high level of quality and continuing to improveSubcontract temporary capacity Strategy Details Level Chase Strategy Strategy Production Production rate equals is constant demand APP Strategies Pure Strategies Capacity Options — Change Capacity Reactive Strategies 1) changing inventory levels 2) varying work force size by hiring or layoffs 3) varying production capacity through overtime or idle time 4) subcontracting




Linking Long Term Capacity Management For Manufacturing And Service Operations Sciencedirect




Chapter 10 Operations Management Fundamentals Of Business
Engaging in the promotional activities, introducing new ways by which product value can be increased, which in turn increases the production rate which leads to maximum capacityImproving Availability Is Much More Than Maintenance By R Keith Mobley, Life Cycle Engineering Many confuse availability with equipment reliability In reality, it is only one part of the calculation Availability is the actual time that the machine or system is capable of production as a percent of total planned production timeA Stable workforce, variable work hours B Chase C Level D Full employment E Skill maintenance




Aggregate Planning Studiousguy




Confluence Mobile Digital Logistics Capacity Assessments
ECONOMIC ORDER QUANTITY (EOQ) MODEL The economic order quantity (EOQ) is the order quantity that minimizes total holding and ordering costs for the year Even if all the assumptions don't hold exactly, the EOQ gives us a good indication ofOn the other hand, the last two costs, depreciation and supervision, are fixed costs and are assumed to be constant over the entire relevant range of activity meaning they do not change based on volume The table below shows the calculations for units produced at 70% capacity and calculates the variable cost per unit for all variable costs The level strategy is considered a traditional aggregate planning method that maintains a steady production rate as well as the level of the workforce by continuing consistent human resources and production in the organization It is best suited where the inventory carrying costs are not high and are adopted by mainly manufacturing companies
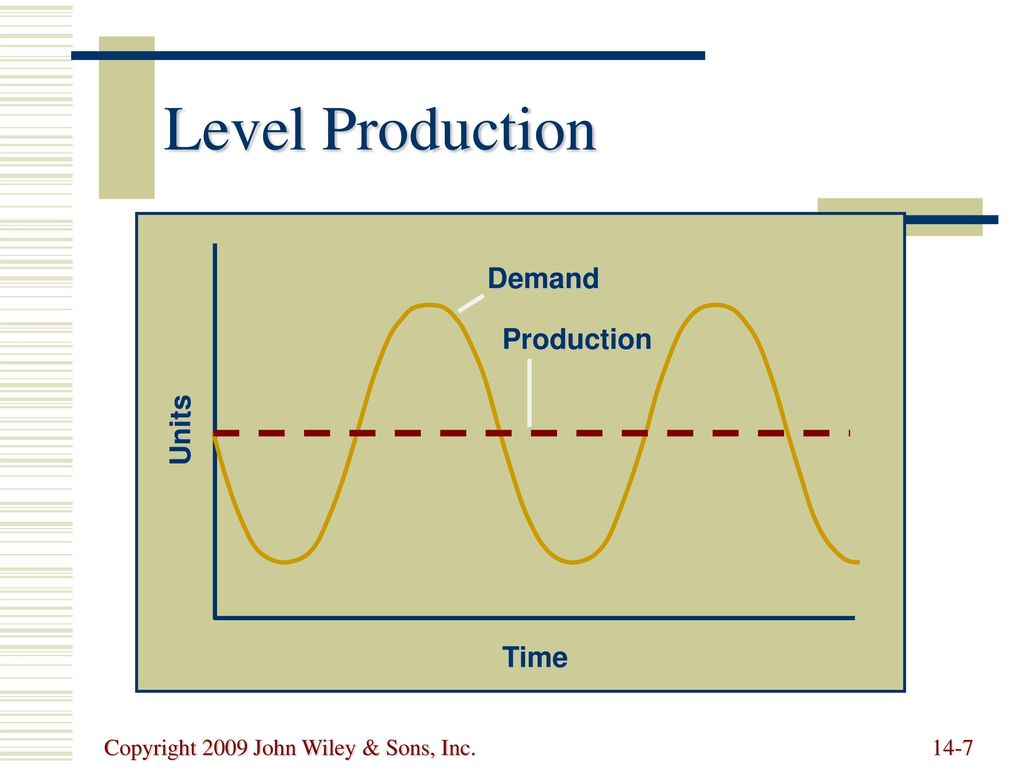



Sales And Operations Planning Ppt Download




Chapter 3 Aggregate Planning Steven Nahmias Ppt Video Online Download
Pushing or pulling arm or leg controls;The other names used for flexible budget are variable budget and sliding scale budget In flexible budget, budgeted figures can be changed according to the level of activity Eg – Budget was prepared for 60% production capacity but in actual 50% or 70% production capacity was usedProduction Management 101 Production, Capacity and Material Planning a Production plan `quantities of final product, subassemblies, parts needed at distinct points in time a To generate the Production plan we need `endproduct demand forecasts `Master production schedule a Master production schedule (MPS) `delivery plan for the
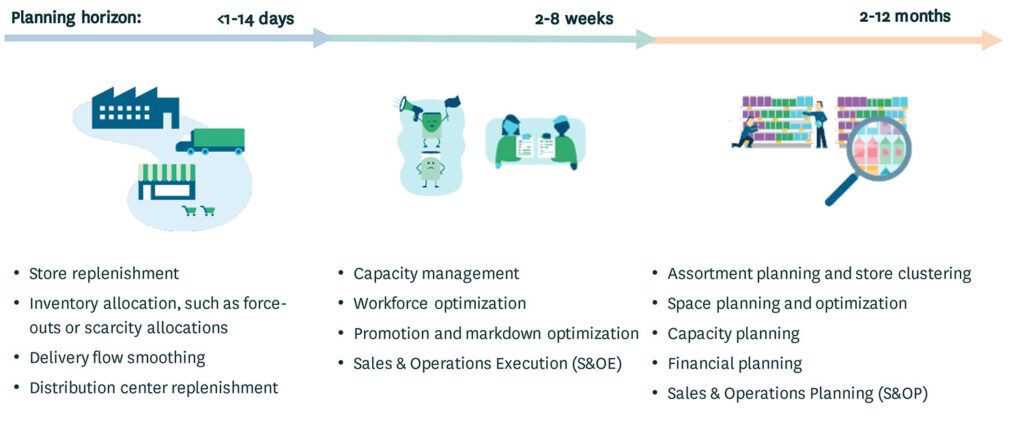



Best Practices For Managing Grocery Retail Supply Chains
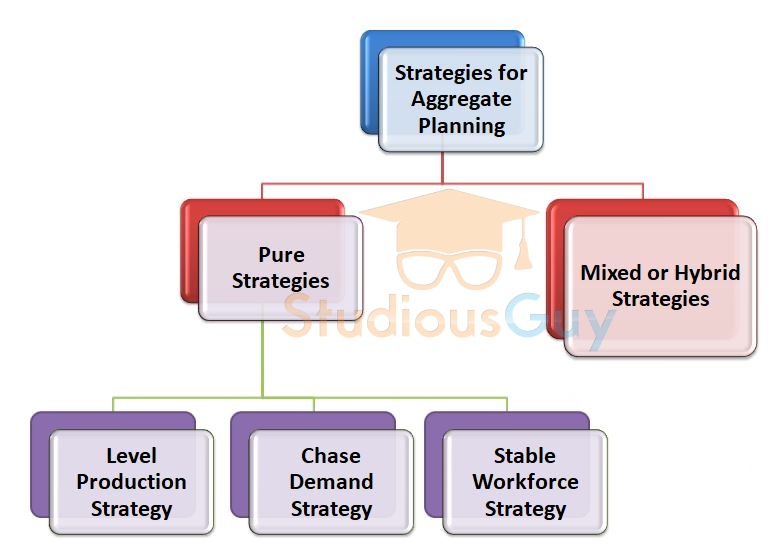



Aggregate Planning Studiousguy
The level capacity strategy involves maintaining stable workforce level and output rates over the planning horizon This allows the firm to maintain inventory levels of finished products higher than expected in situations of low demand variability As demand increases above the steady output rate, the firm can continue to maintainEnter the standard capacity level at which a production line usually operates Capacity is stated in units per hour For example, if the constant is set to Y, the value of this field is 80 percent, It is the ratio of the direct time charged for production activities to the planned hoursList the capacity options in aggregate planning 1 Hire and lay off workers 2 Overtime/slack time 3 parttime workers 4 Inventories 5 Subcontracting 5 List the main strategies for meeting uneven demand 1 Maintain a level of workforce 2 Maintain a steady output rate 3 Match demand period by period 4 Use a combination of decision
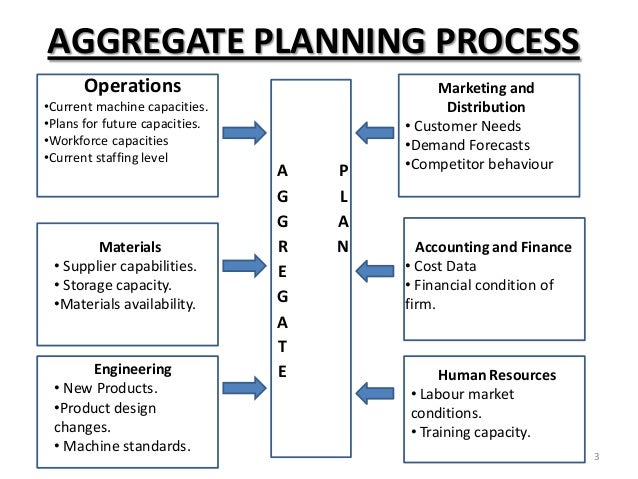



Models Of Aggregate Planning




Orange Presents Its New Strategic Plan Engage25 Orange Business Services
Required If the required rate of return of investment in inventories is 15%, should the company implement the new production plan?Production each year, the fishery is sustainable If stock size is maintained at half its carrying capacity, the population growth rate is fastest, and sustainable yield is greatest (Maximum Sustainable Yield) K = unfished stock biomass at carrying capacity r = intrinsic rate of stock growth 9 X t denotes the resource stock in time t, F(XBuild models based on estimated changes;




Capacity Planning An Overview Sciencedirect Topics



Myclass Dau Edu cswebdav Xid 4 2
The general term " Production" is the creation of new organic matter When a crop of wheat grows, new organic matter is created by the process of photosynthesis, which converts light energy into energy stored in chemical bonds within plant tissue ThisThe goal is to produce intermediate goods at a constant rate so that further processing may also be carried out at a constant and predictable rate Where demand is constant, production leveling is easy, but where customer demand fluctuates, two approaches have been adopted 1) demand leveling and 2) production leveling through flexible productionAnswer all questions and show necessary work Please be brief This is an open books, open notes exam
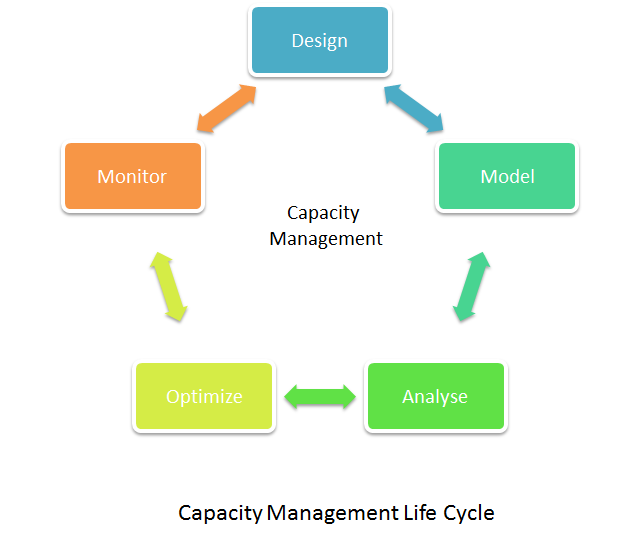



What Is Capacity Management Definition And Faqs Omnisci




Linking Long Term Capacity Management For Manufacturing And Service Operations Sciencedirect
Production Planning and Control Scientific task planning ensures timely supply of inputs, proper maintenance of plant, efficient work scheduling and regulation of daytoday ' activities in the plant It facilitates full utilization of plant capacity and achievement of production targets Technique # 5 Workers' Participation in Management With the level capacity approach, production capacity is held constant over the planning horizon;I maintain our capacity at a level of 17,000 transactions per day" Why the big difference in capacity management in the same firm?
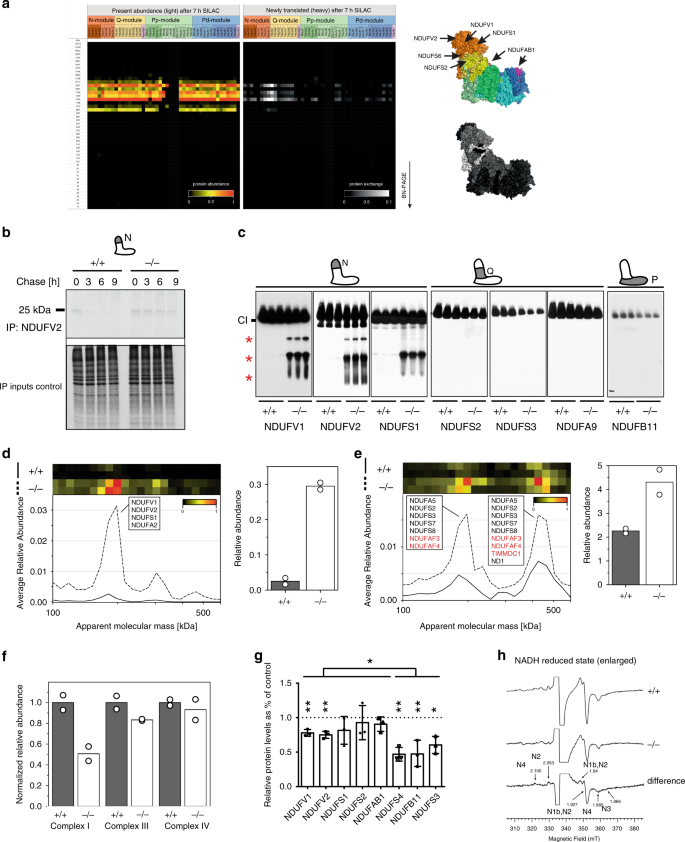



A Salvage Pathway Maintains Highly Functional Respiratory Complex I Nature Communications
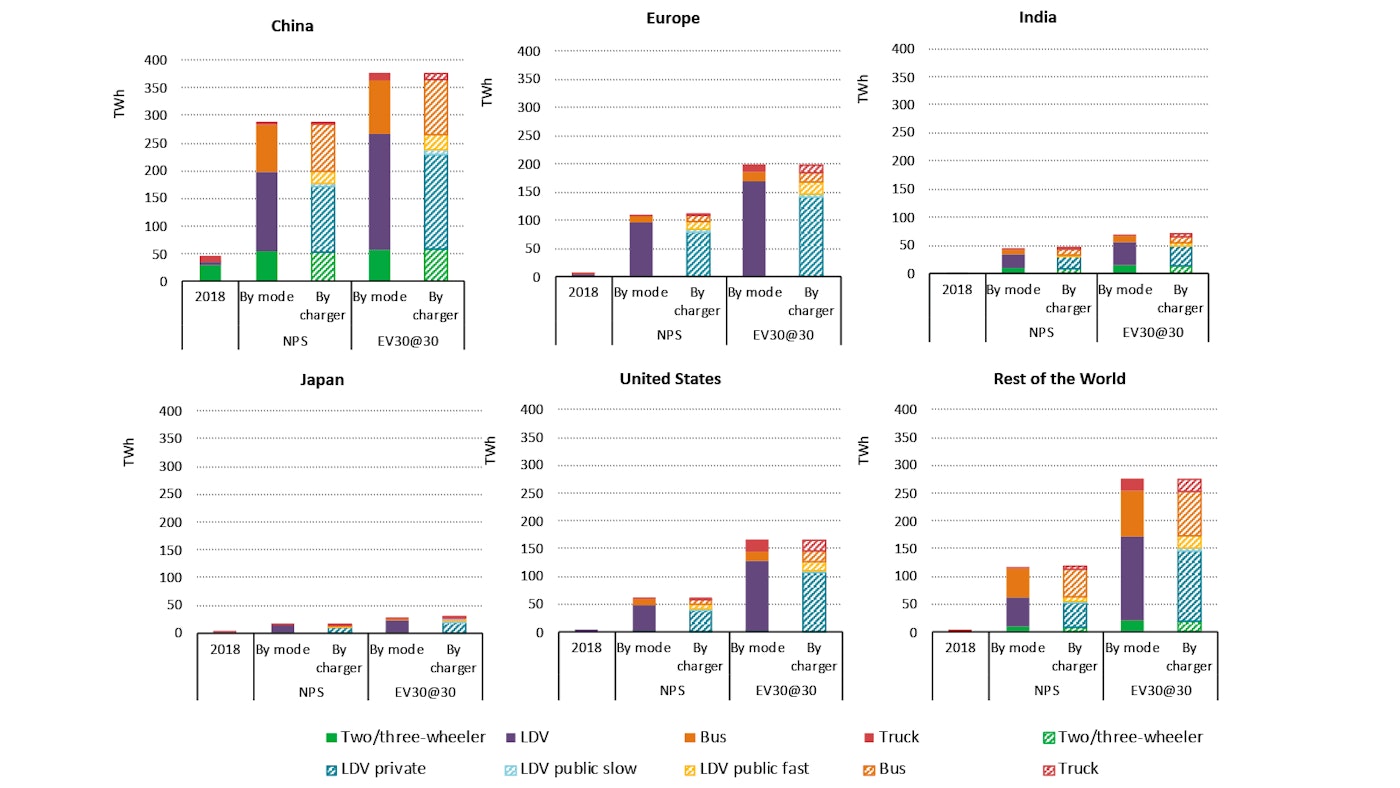



Global Ev Outlook 19 Analysis Iea
{ The Justintime production plan, also known as the chase plan, consists in changing the production rate to exactly satisfy demand The idea is consistent with the JIT production philosophy and results in low holding costs but may result in high cost of adjusting the production rate, ie, high flring and hiring costs or high idle timesAlthough maintaining piston production internally would require some level of process investment in Years 3 through 10, the team believes any projections past Year 2 contain too much uncertainty (Conducting a net present value for expected savings from outsourcing, if they exist, is beyond the scope of this assignment) Insourcing CostsStandard Capacity Enter the standard capacity level at which a production line usually operates Capacity is stated in units per hour if the constant is set to Y, the value of this field is 80 percent, This value usually refers to machine use It is the ratio of the direct time charged for production activities to the planned hours
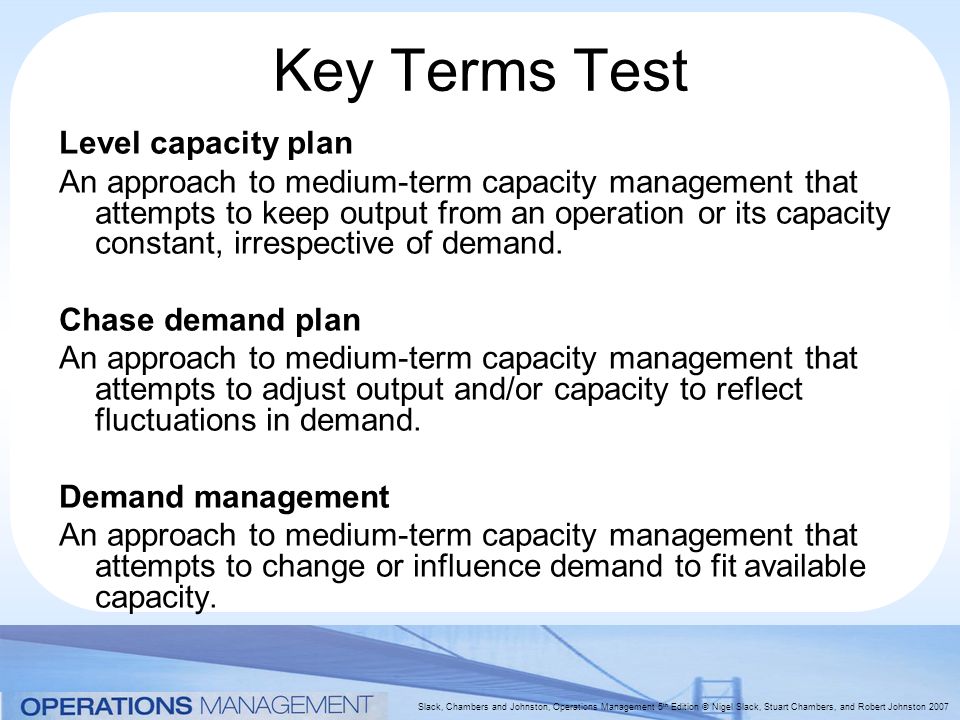



Capacity Planning And Control Ppt Video Online Download
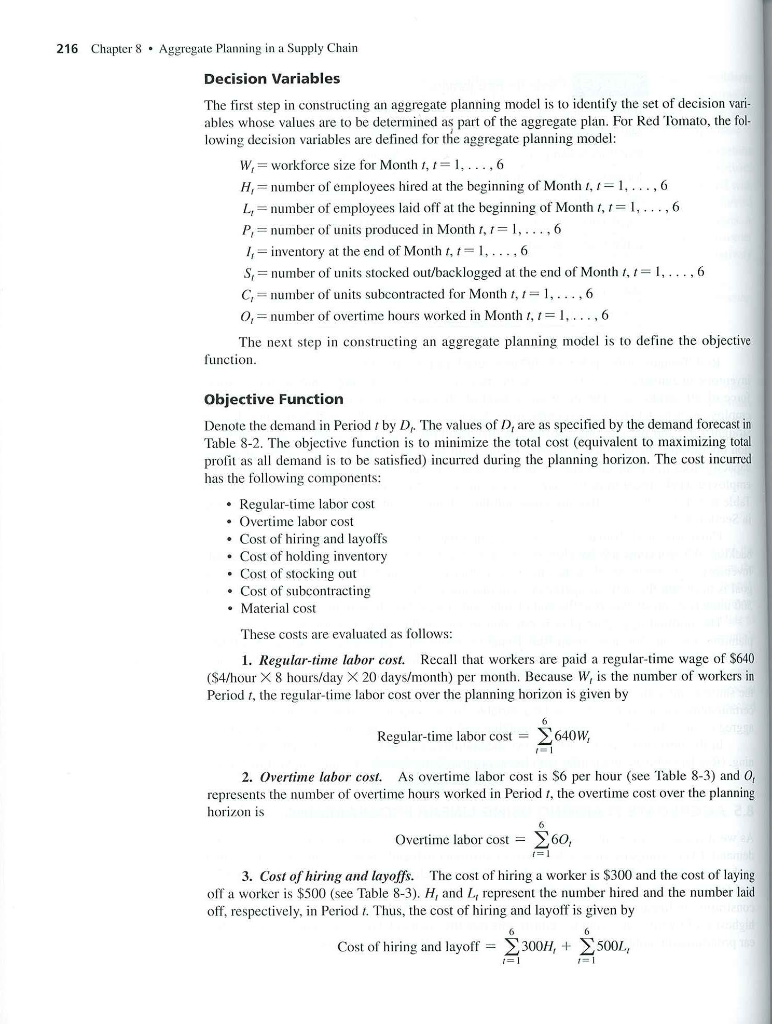



Aggregate Planning In A Supply Chain 214 Chapter 8 Chegg Com
Maintaining a stable workforce working at a constant output rate while shortages and surpluses are absorbed by fluctuating inventory levels, order backlogs, and allowing lost sales is which of the following production planning strategies?Example 49 Daily standard production rate of a power shovel A power shovel with a dipper of one cubic yard capacity has a standard operating cycle time of 30 seconds Find the daily standard production rate of the shovel For C e = 1 cu yd, T e = 30 sec and H e = 8 hours, the daily standard production rate is found from Eq (46) as followsInvestment (tooling cost) which then permits production of the remainder of the group without additional tooling cost 4 Level Production To a greater extent than is common in most manufacturing operations, there is a strong incentive to maintain a nearly level manufacturing rate This arises




Capacity Planning An Overview Sciencedirect Topics
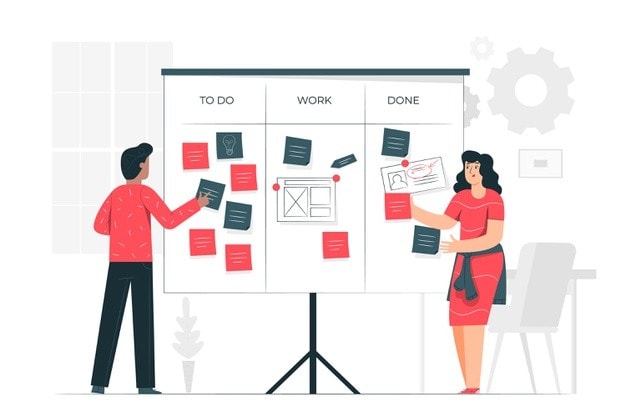



Aggregate Planning Definition Importance Strategies Management And Advantages
After Plan cost split, the next step if Plan price calculation Plan price calculation basically helps to calculate "Plan Activity Rate" The activity rate could be in two parts, ie Fixed Activity rate and Variable Activity rate Fixed Activity rates are calculated based on Plan Cost (Fixed) Split, during KSS4, divided by Capacity At 1001 percent of its 17 average, total industrial production in June was 98 percent above its yearearlier level but 12 percent below its prepandemic (February ) level Capacity utilization for the industrial sector rose 03 percentage point in June to 754 percent, a rate that is 42 percentage points below its longrun (1972Chapter 14 Question & Answers 1 Advanced costing methods ROCHE (ABC) Questions Roche has recently set up a small business, which manufacturesthree different types of chair to customer order Each type is producedin a single batch per week and dispatched as individual items The sizeof the batch is determined by the weekly customer orders
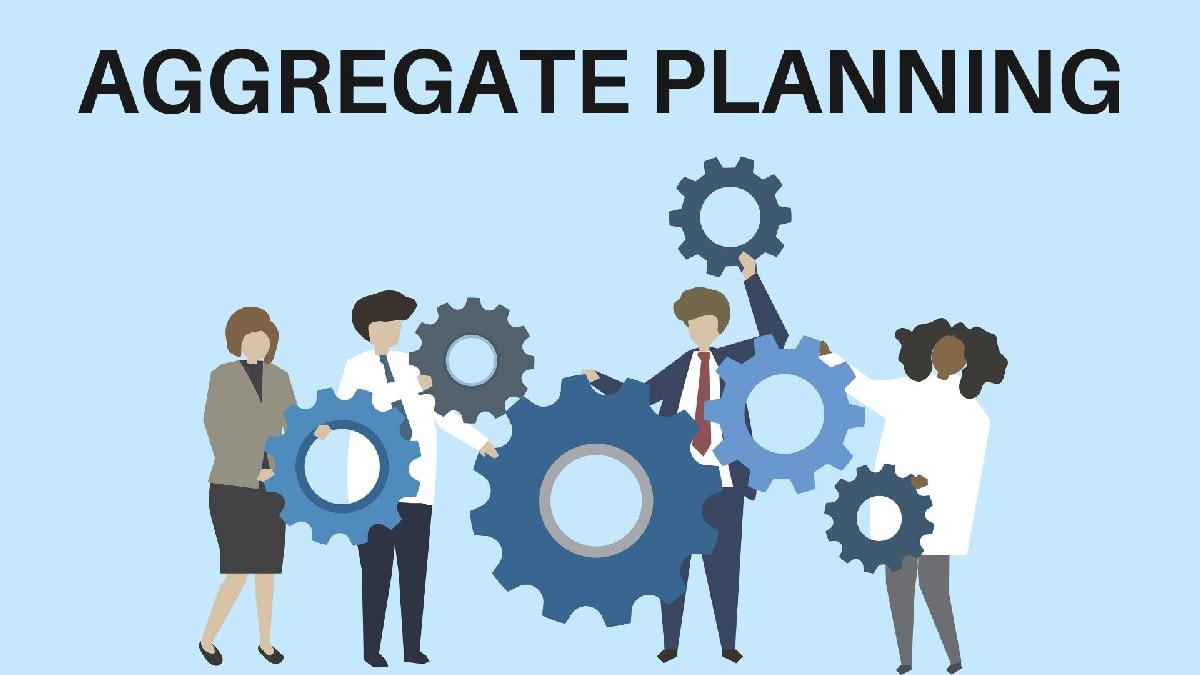



Aggregate Planning Definition Importance Strategies Management And Advantages




Chapter 17 Questions Answers
And the difference between the constant production rate and the varying demand rate is made up by inventory, backlog, overtime labor, part time labor, temporary labor, and/or subcontracting An MTO operation usually adopts a hybrid approach of bothProduction Rate In manufacturing, the number of goods that can be produced during a given period of time Alternatively, the amount of time it takes to produce one unit of aIdentify trends to estimate future utilization requirements;
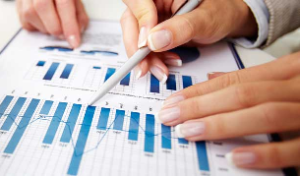



Production Planning Meaning And Different Activities Involved
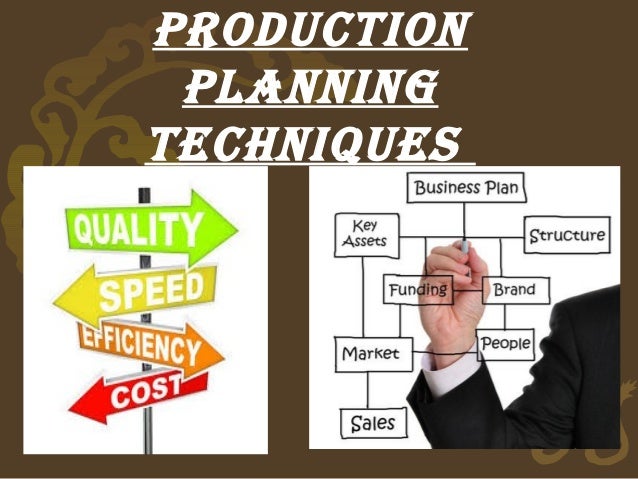



Production Planning Techniques Aggregate Planning
Variable costs vary in a linear fashion with the production level However, when stated on a per unit basis, variable costs remain constant across all production levels within the relevant range The following two charts depict this relationship between variable costs and output volume A good example of a variable cost is materialsSupply Chain Management Chapter 19 The aggregate operations plan translates annual and quarterly business plans into broad labor and output plans for the intermediate term of 3 to 18 months The objective of the aggregate operations plan is to ensure that the marketing and sales plans are realistic Nice work! The medicalvocational rules use the subcategory "younger individual age 4549" in the sedentary medicalvocational table and "closely approaching retirement age" in the medium medicalvocational table For the medicalvocational guidelines, see DI The age categories and subcategories are a Age categories 1




Aggregate Planning Strategy Organization Levels System Examples Model Type Company System




Global Ev Outlook 19 Analysis Iea
Current Capacity is the amount you can produce using your equipment as is (at its current effectiveness) and within your current production schedule Target Capacity is the amount you will produce when you reach your OEE target (reducing Equipment Losses) and schedule more production time (reducing Schedule Losses) Remember though – many manufacturers can improve capacity2 Economic Order Quantity Lito Corporation has been buying product A in lots of 1,0 units which represents a four month's supply The cost per unit isAnd develop and maintain a capacity plan




Spring Batch Reference Documentation
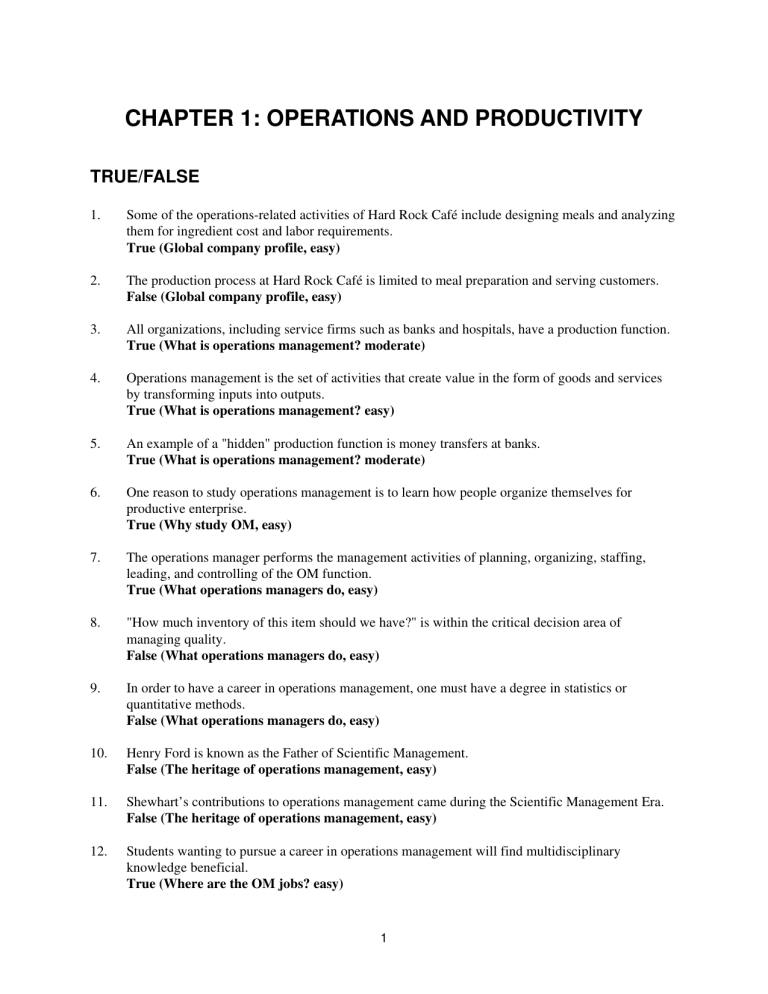



Test Bank For Heizer Operations Management 9e
Dr Eduardo Calixto, in Gas and Oil Reliability Engineering (Second Edition), 16 Stock Policy Stock level is an important issue that must be considered because it can affect system availability when repair is delayed more than necessary because a component is not in stock and it is necessary to purchase one In such cases the system is unavailable, and to avoid this the stock policy must beIt is unlikely that an economy or company will function at a 100% capacity rate as there are always hurdles in the production process (such as the malfunction of equipment or unequal distribution of resources) A rate of 85% is considered the optimal rate for most companies The capacity utilization rate is used by companies that manufacture physical products and not servicesThis chapter considers how capacity can be provided, adjusted and managed in order to satisfy the demand of the consumer and meet the objectives of the operation as efficiently as possible 2 Capacity Management Capacity management affects all areas of an operation Capacity measures the rate that the operation can transform inputs into outputs




Models Of Aggregate Planning



1
Aggregate Planning By Dr Debadyuti Das We use your LinkedIn profile and activity data to personalize ads and to show you more relevant adsSome proactive capacity management and planning activities include utilize network capacity management, production capacity management and storage capacity management tools to predict network, production, and storage needs;A level strategy seeks to produce an aggregate plan that maintains a steady production rate and/or a steady employment level In the context of the problem posted by you following the level strategy means incurring additional subcontracting costs at least twice This is to offset the shortfall in production because of the level strategy




Kup9 Maintains Root Meristem Activity By Regulating K And Auxin Homeostasis In Response To Low K Embo Reports



Www Diva Portal Org Smash Get Diva2 Fulltext01 Pdf
Level Strategy As the name suggests, level strategy looks to maintain a steady production rate and workforce level In this strategy, organization requires a robust forecast demand as to increase or decrease production in anticipation of lower or higher customer demand Advantage of level strategy is steady workforce
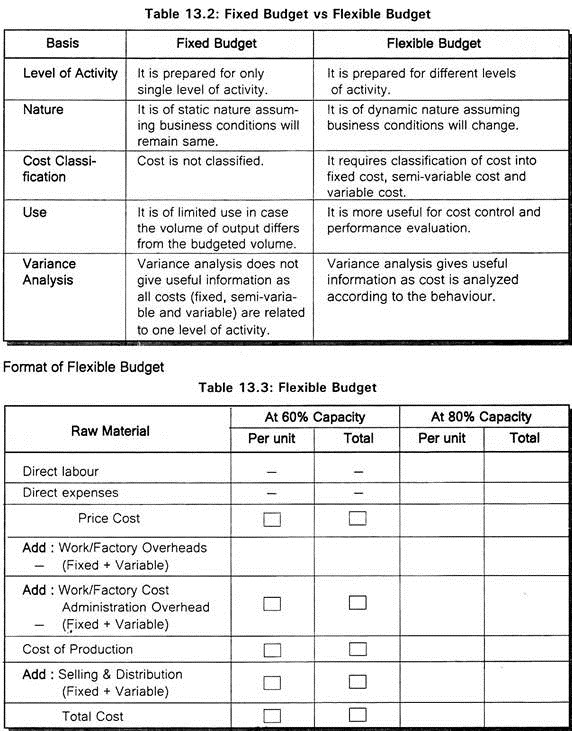



Types Of Budget In Accounting 25 Major Types



Http 1 160 97 198 8080 Xmlui Bitstream Handle 436 Operations Management kumar a a and suresh n Pdf Sequence 1
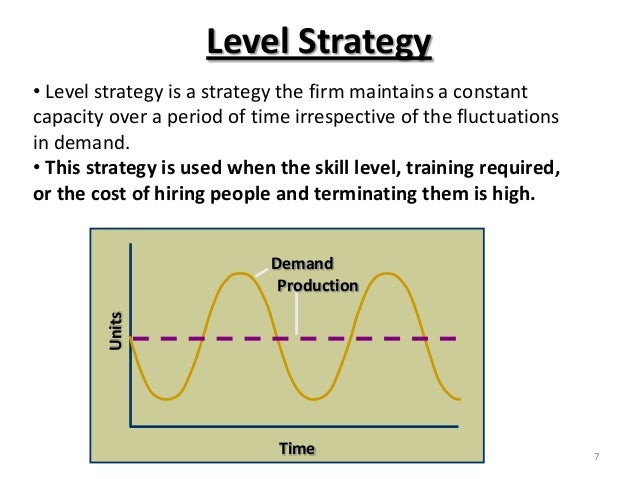



Models Of Aggregate Planning




Aggregate Planning Strategy Organization Levels System Examples Model Type Company System



Http 1 160 97 198 8080 Xmlui Bitstream Handle 436 Operations Management kumar a a and suresh n Pdf Sequence 1




Chapter 17 Questions Answers



Www Mdpi Com 71 1050 12 9 3791 Pdf




Strategic Capacity Planning Aggregate Planning Ppt Video Online Download



Myclass Dau Edu cswebdav Xid 4 2




Sales And Operations Planning Aggregate Planning Production Planning Operations Planning How To Meet Effectively And Efficiently Forecasted Requirements Ppt Video Online Download
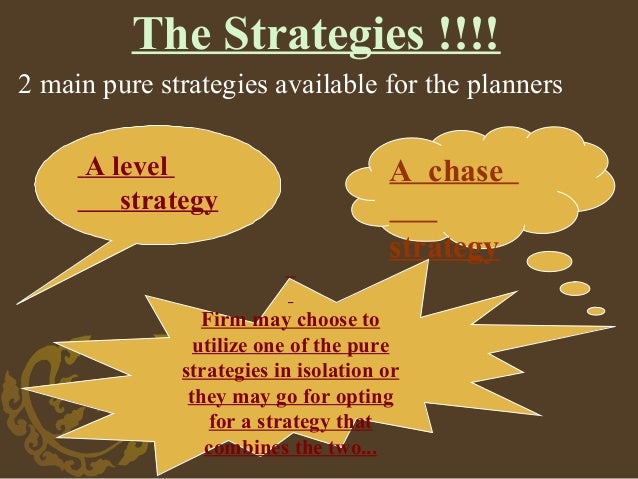



Production Planning Techniques Aggregate Planning




Module 6 Flashcards Quizlet
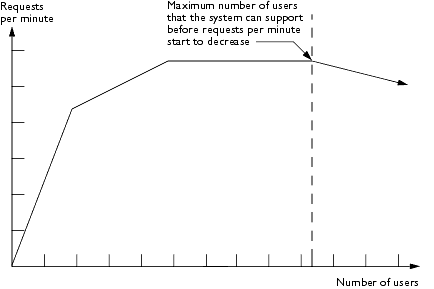



Deployment Guide Determining System Capacity
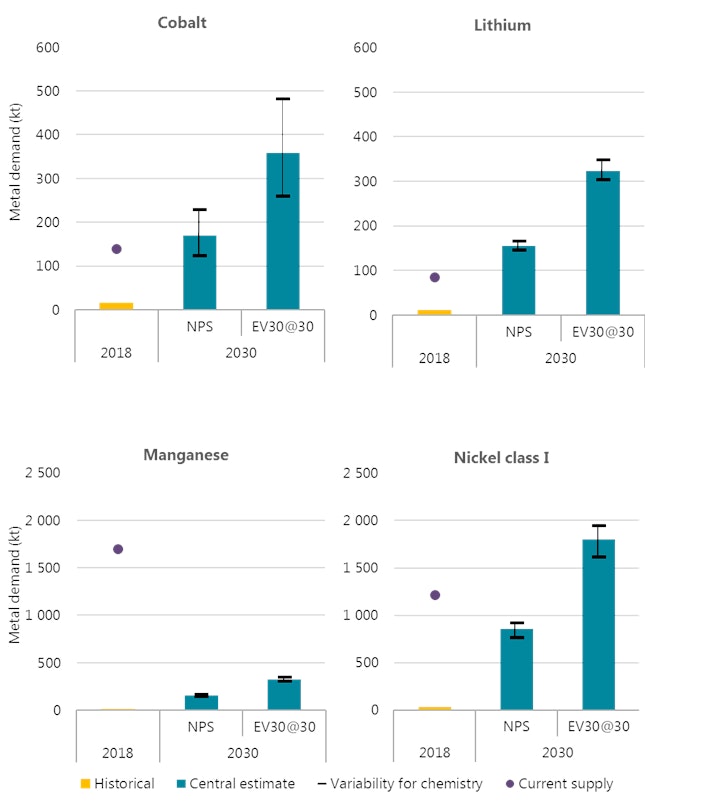



Global Ev Outlook 19 Analysis Iea



Myclass Dau Edu cswebdav Xid 4 2
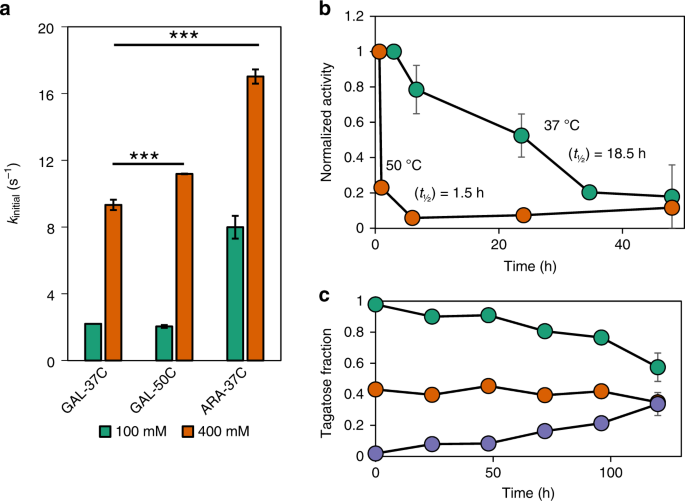



Galactose To atose Isomerization At Moderate Temperatures With High Conversion And Productivity Nature Communications



Solved Number Of Employees At The Start Of The Tint Quarter 126 Coat Per I Plcyee Number Of Units Produced Per Employee Overtime Demand For The Rst Course Hero



Uninote Ecommerce S3 Eu West 2 Amazonaws Com Capacity management Pdf
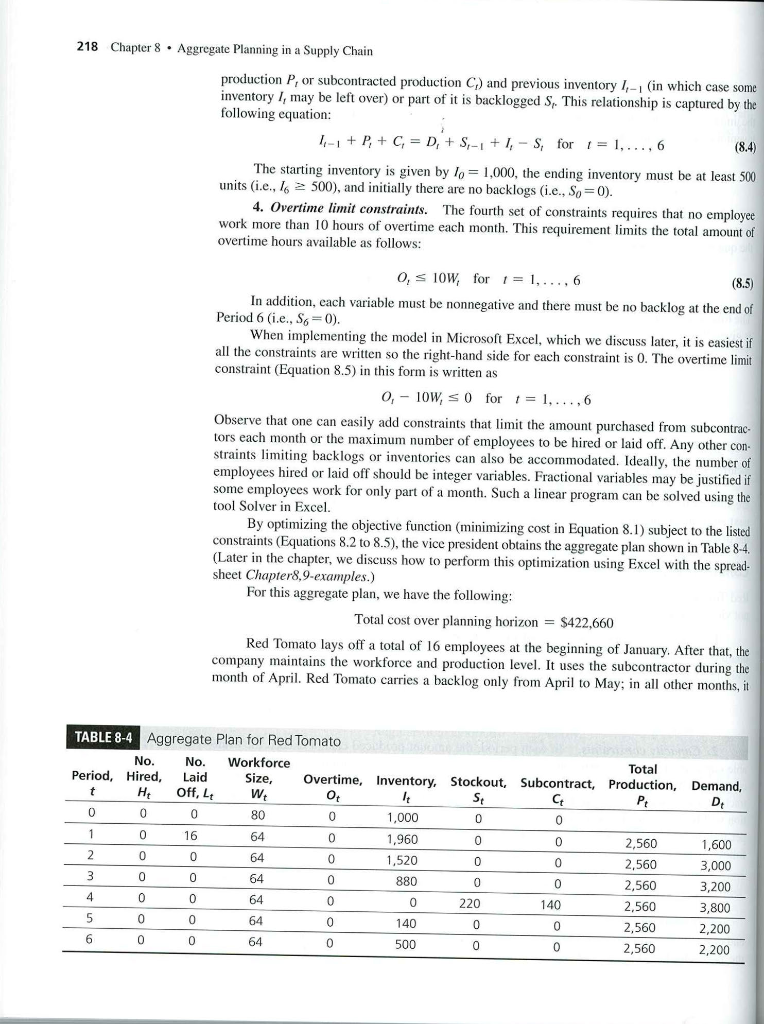



Aggregate Planning In A Supply Chain 214 Chapter 8 Chegg Com
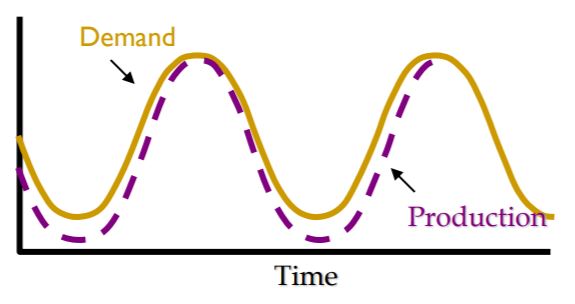



Aggregate Planning Studiousguy
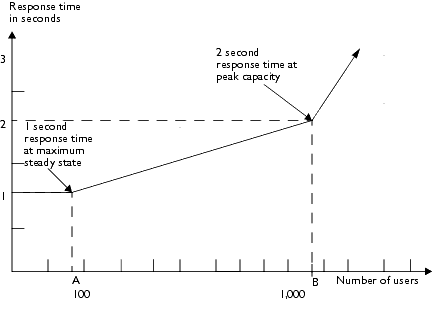



Deployment Guide Determining System Capacity
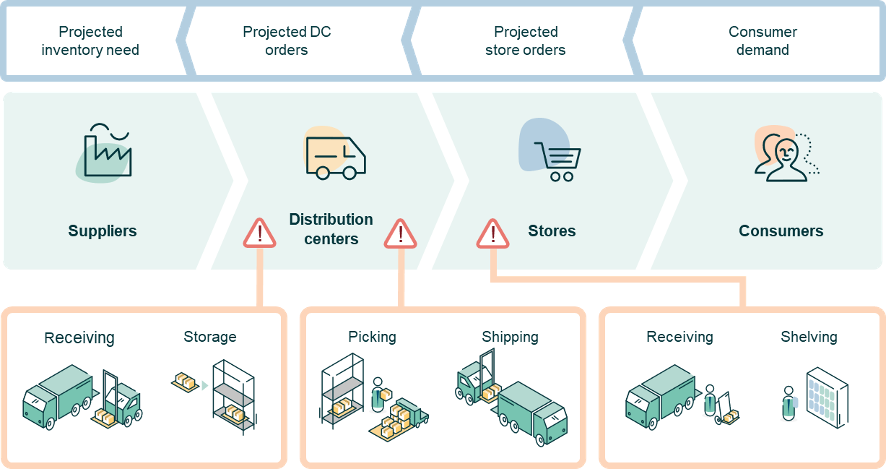



Best Practices For Managing Grocery Retail Supply Chains
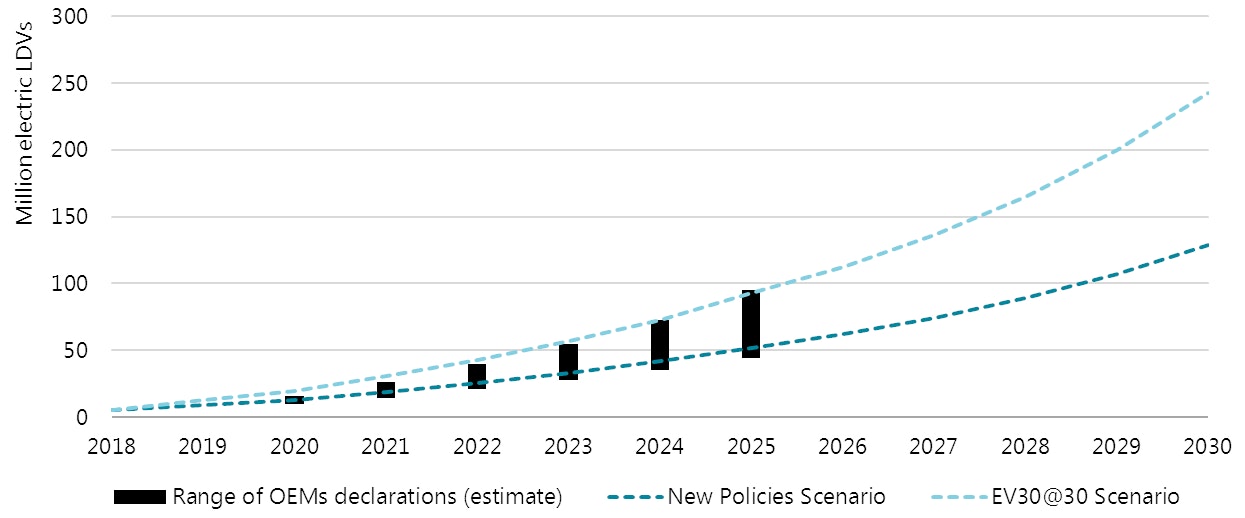



Global Ev Outlook 19 Analysis Iea




Kup9 Maintains Root Meristem Activity By Regulating K And Auxin Homeostasis In Response To Low K Embo Reports
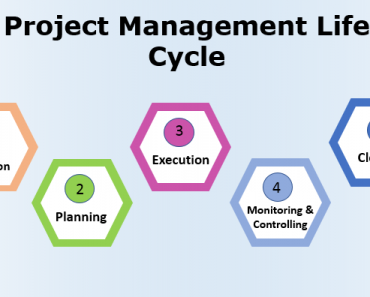



Aggregate Planning Studiousguy
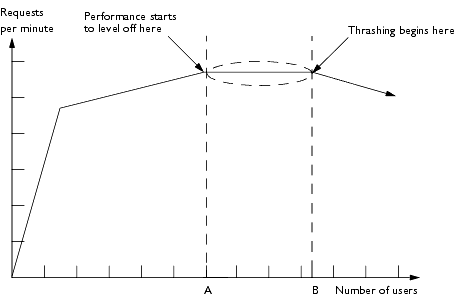



Deployment Guide Determining System Capacity



Myclass Dau Edu cswebdav Xid 4 2



Perso Crans Org Fortineau Ressources Maxnce Nouchet Introduction to materials management Pdf



Regulations Easa
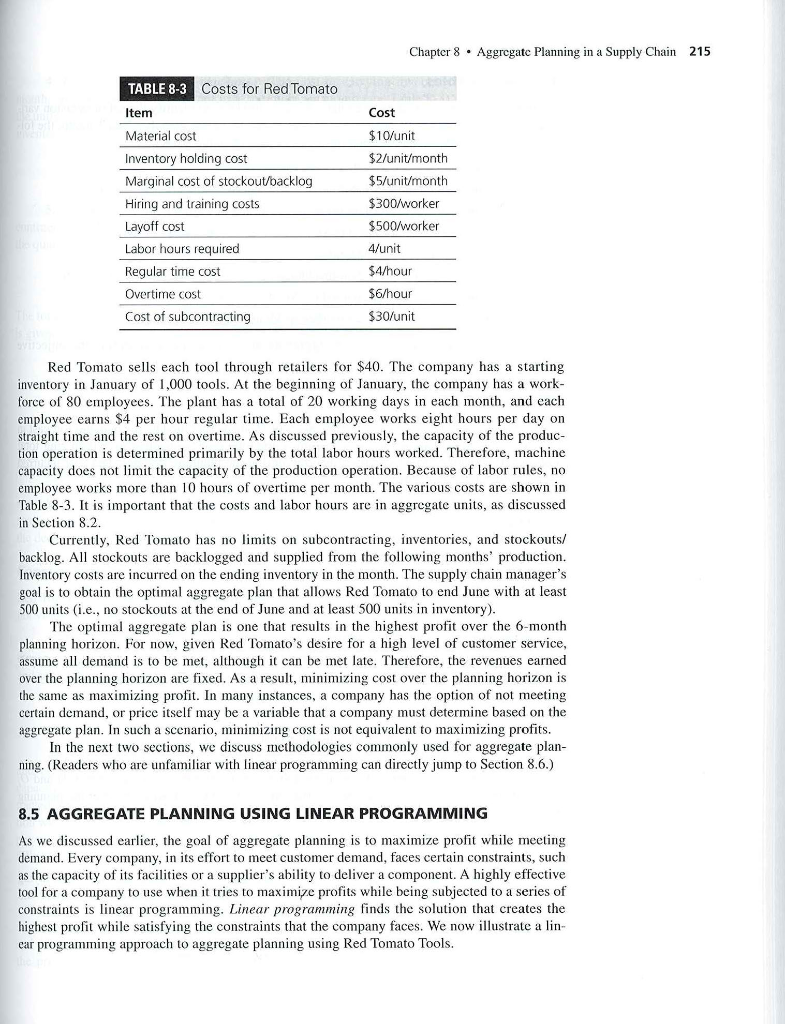



Aggregate Planning In A Supply Chain 214 Chapter 8 Chegg Com



1



1



Http Ddegjust Ac In 17 Uploads 11 Pom 326 Pdf




The Economy Unit 15 Inflation Unemployment And Monetary Policy



Covid Economics Centre For Economic Policy Research




Product Development And Management Strategies Intechopen



Http Ddegjust Ac In 17 Uploads 11 Pom 326 Pdf




Chapter 13 Questions Answers



Www Mdpi Com 71 1050 12 9 3791 Pdf
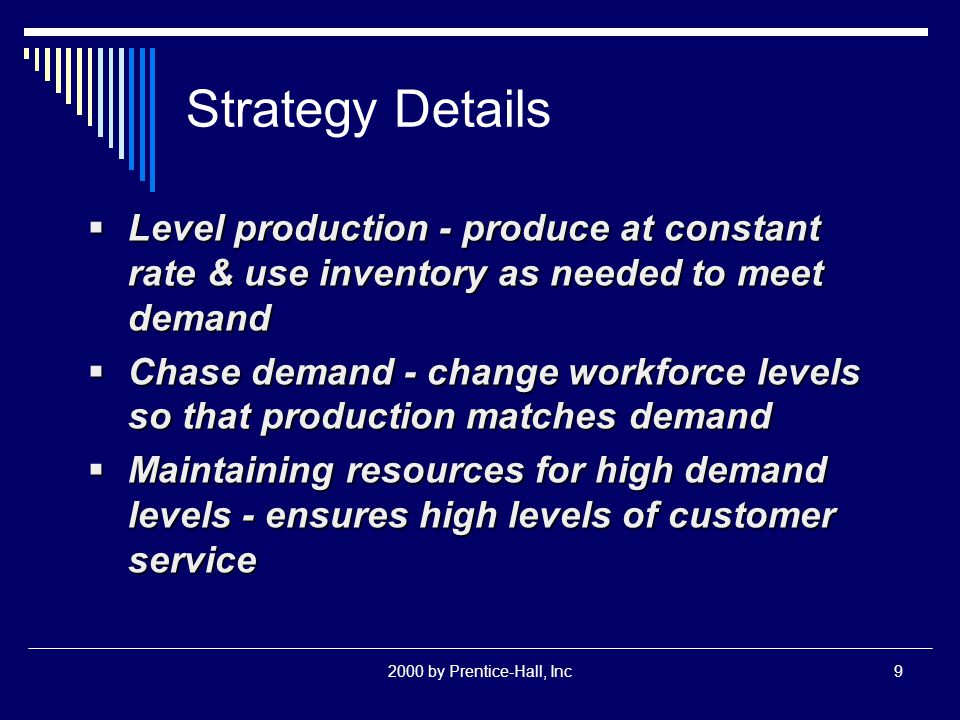



Chapter 9 Capacity Planning 00 By Prentice Hall Inc Ppt Video Online Download




Aggregate Planning Strategy Organization Levels System Examples Model Type Company System
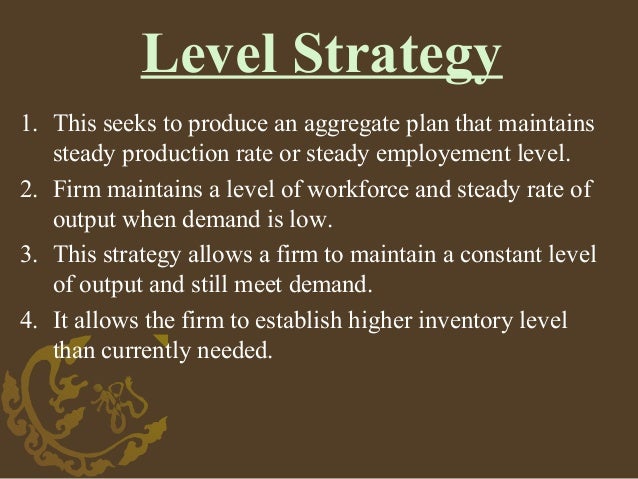



Production Planning Techniques Aggregate Planning
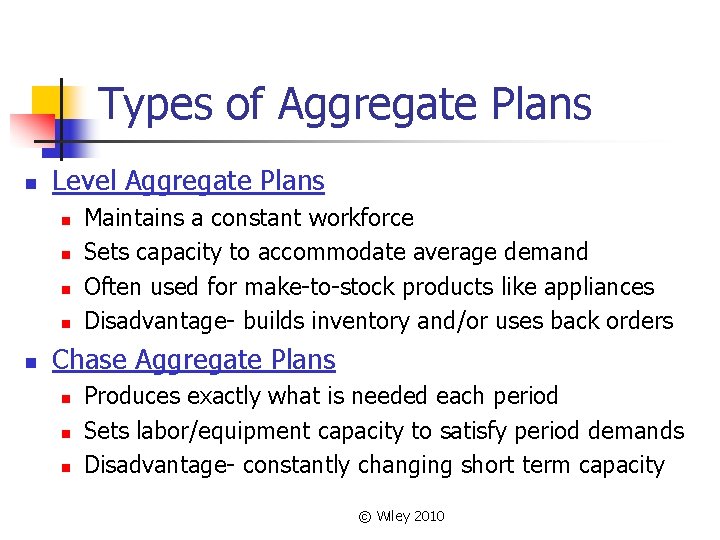



Chapter 13 Aggregate Planning Operations Management By R
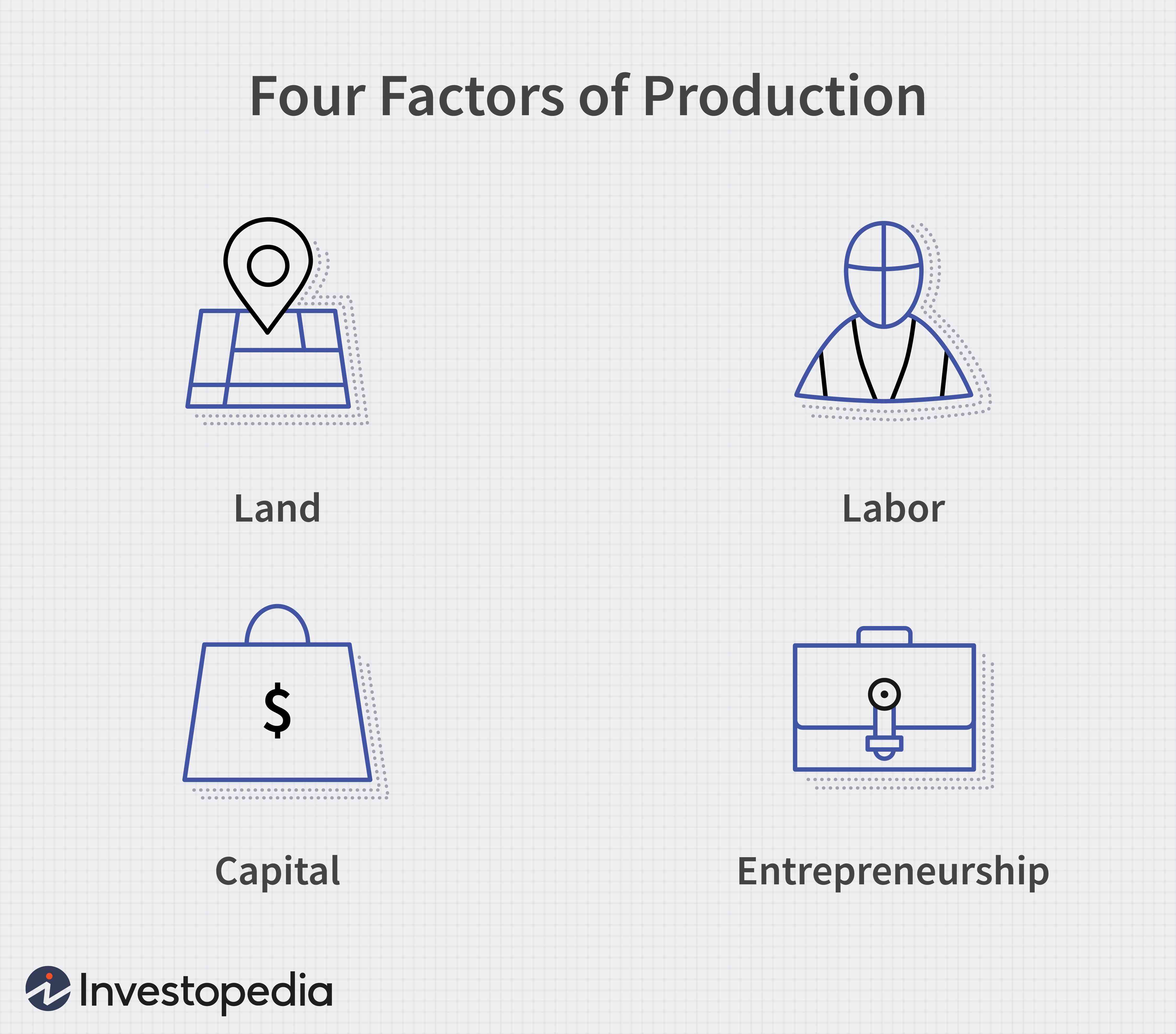



Production Economics Wikipedia



Http Ddegjust Ac In 17 Uploads 11 Pom 326 Pdf



Myclass Dau Edu cswebdav Xid 4 2
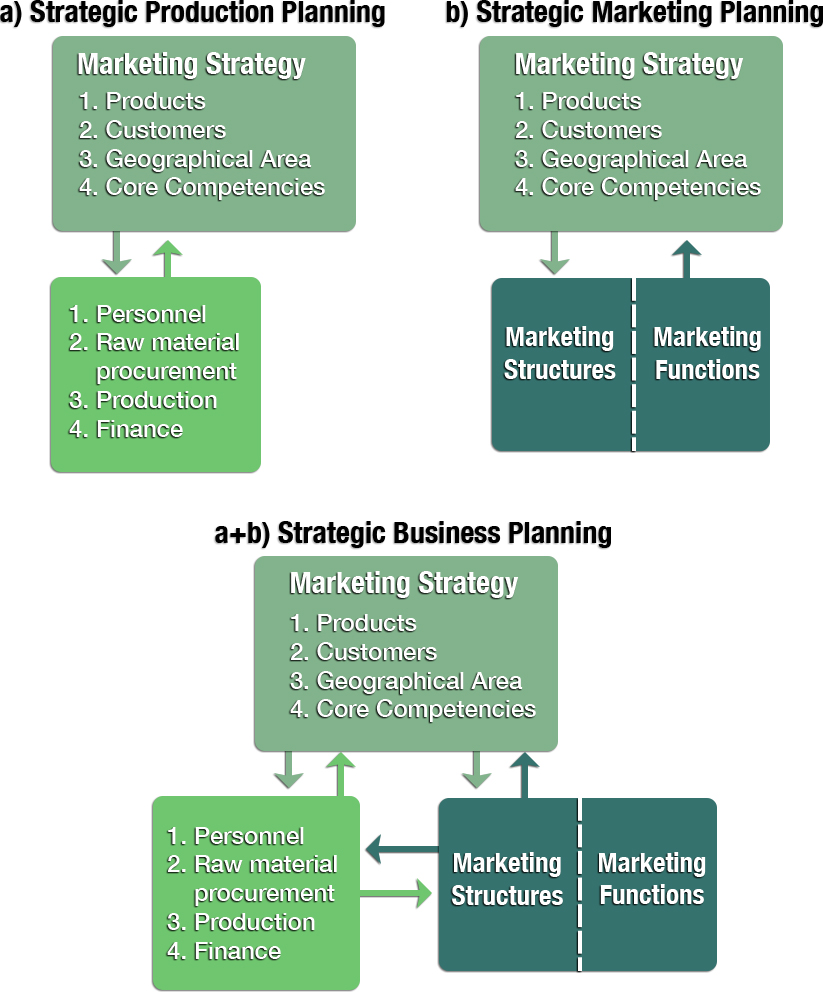



Chapter 4 Strategy And Strategic Planning Strategic Marketing In The Global Forest Industries
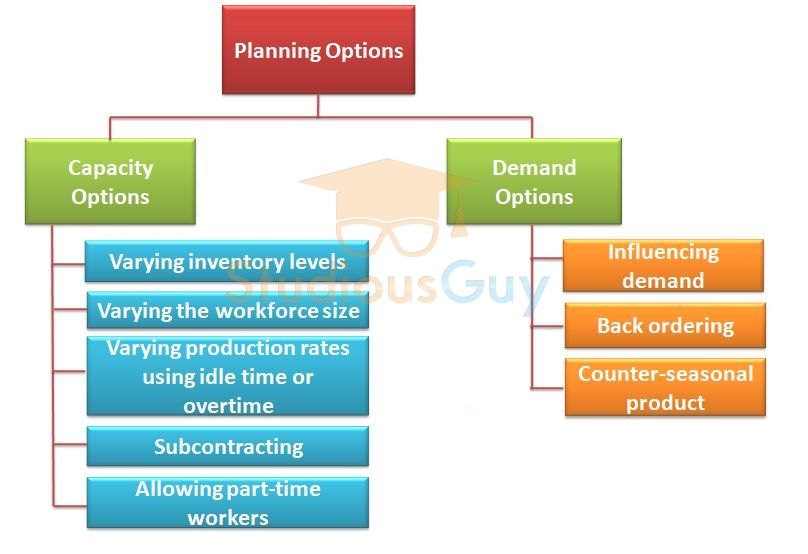



Aggregate Planning Studiousguy



Icmai In Upload Students Syllabus 12 Study Material New Inter Paper9 Pdf



Http Ddegjust Ac In 17 Uploads 11 Pom 326 Pdf



Chapter 42 Heat And Cold
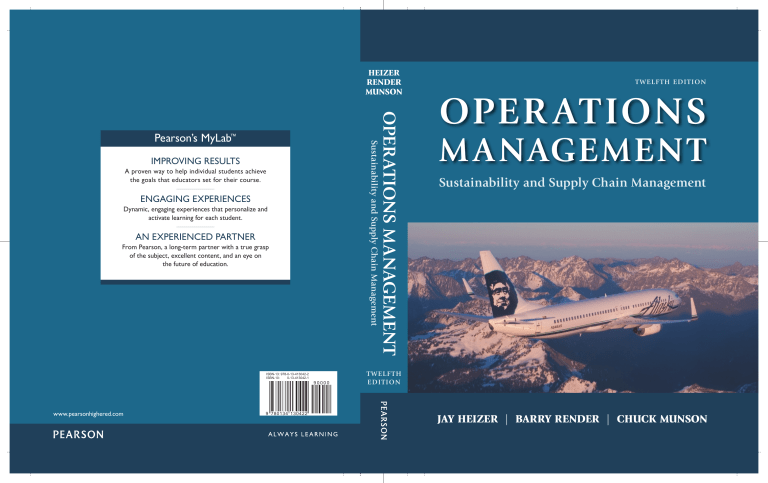



Operations Management Book Capacity Planning Included



Icmai In Upload Students Syllabus 12 Study Material New Inter Paper9 Pdf



Www Dau Edu Guidebooks Shared documents Defense manufacturing management guide for pms Pdf
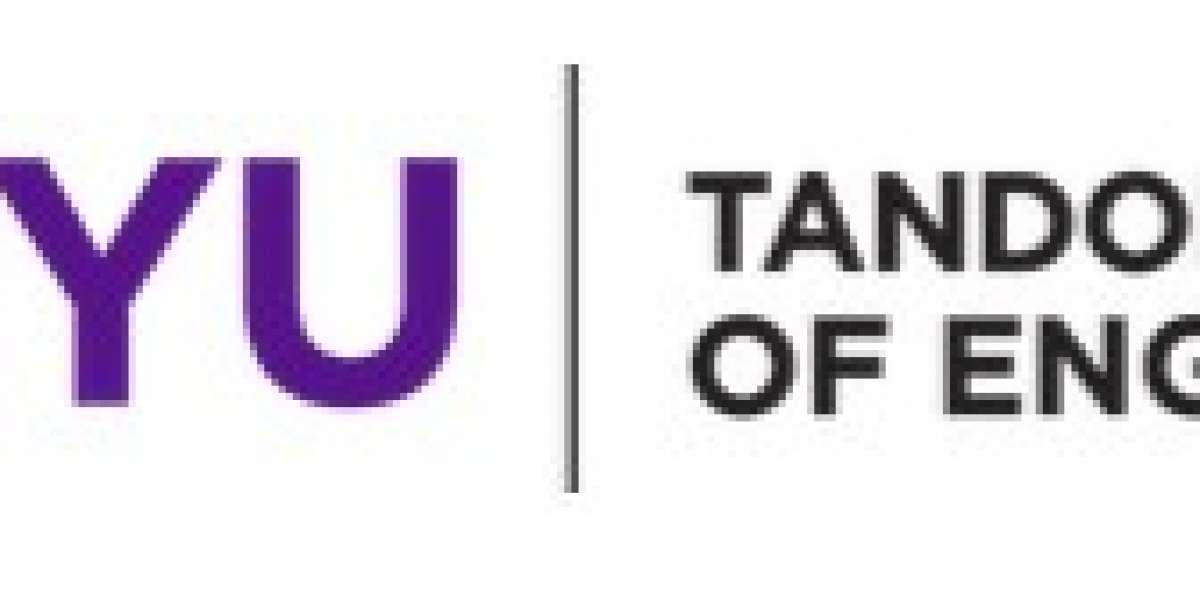



Nike Operations Management




Amp Activated Protein Kinase Is Essential For The Maintenance Of Energy Levels During Synaptic Activation Biorxiv




Kup9 Maintains Root Meristem Activity By Regulating K And Auxin Homeostasis In Response To Low K Embo Reports



Myclass Dau Edu cswebdav Xid 4 2




Match Supply And Demand In Service Industries
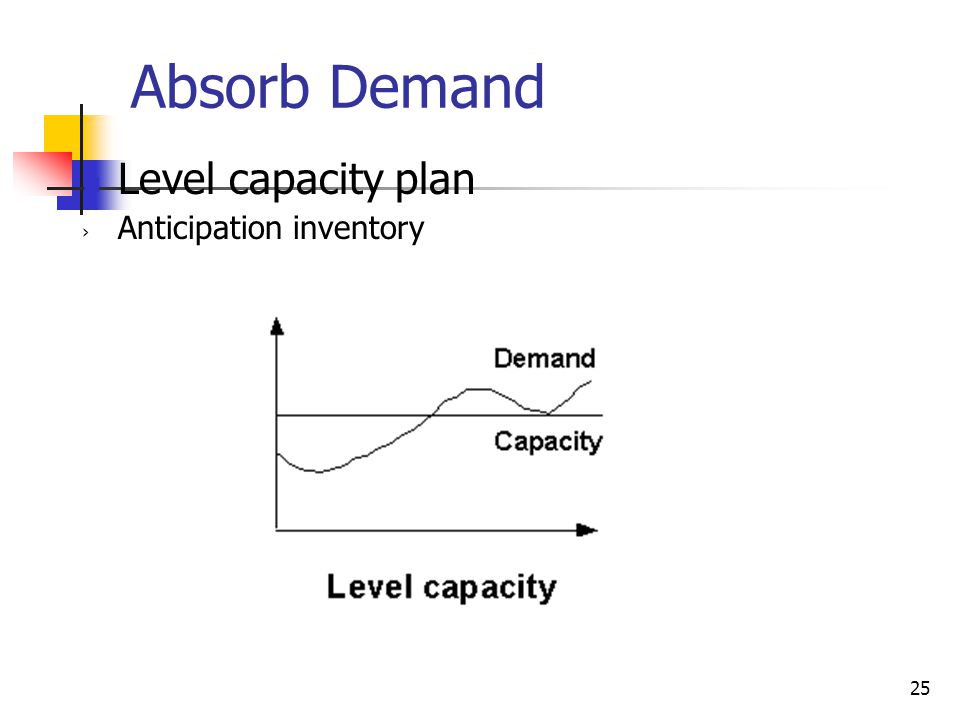



Operations Management Ppt Video Online Download
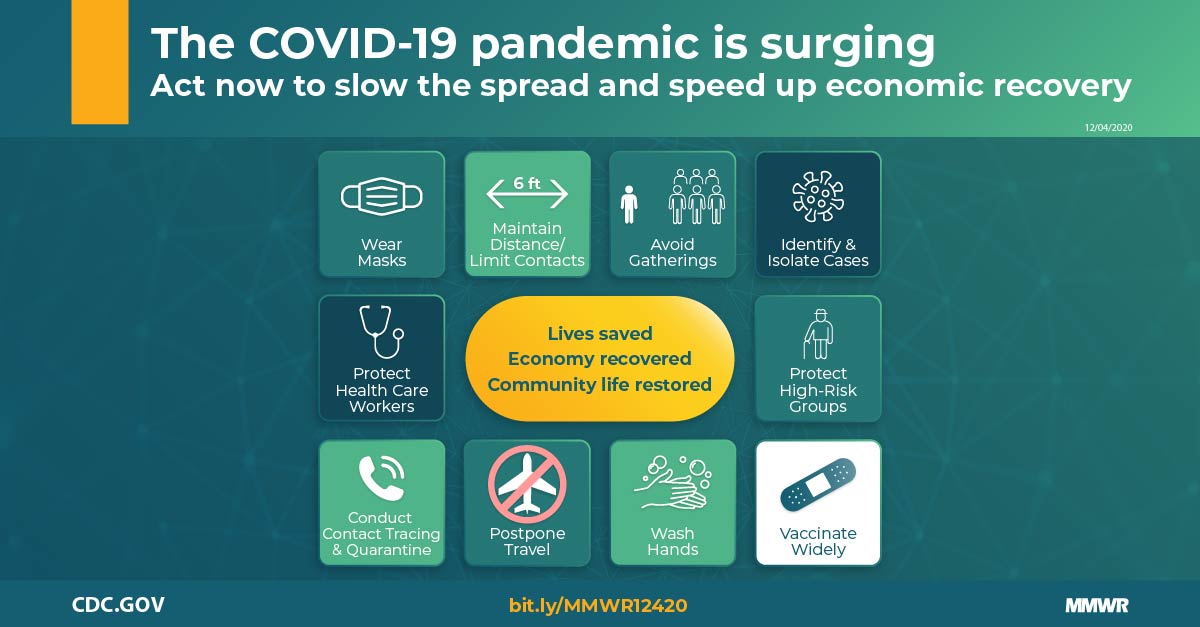



Summary Of Guidance For Public Health Strategies To Address High Levels Of Community Transmission Of Sars Cov 2 And Related Deaths December Mmwr
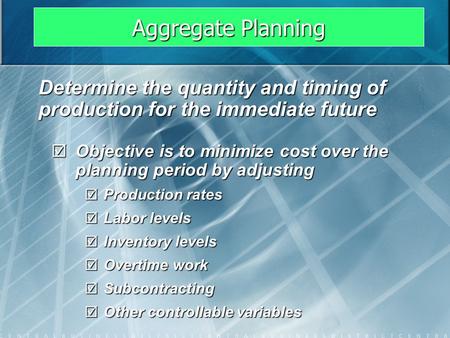



Sales And Capacity Planning Ppt Video Online Download
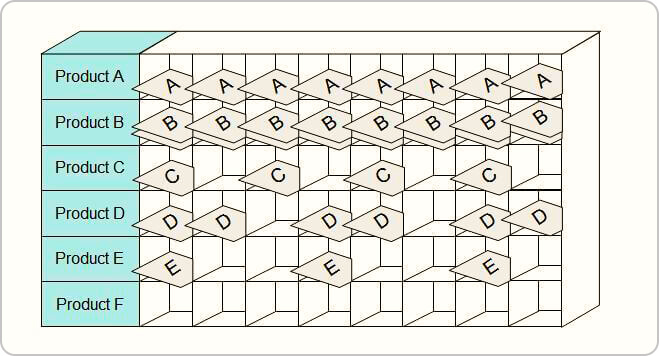



Continuous Flow




Oracle Advanced Supply Chain Planning Implementation And User S Guide



Chapter 42 Heat And Cold



Conceptual Framework For The Strategic Management A Literature Review Descriptive




Product Development And Management Strategies Intechopen



1




Sales And Capacity Planning Ppt Video Online Download
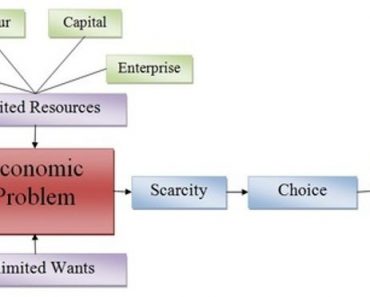



Aggregate Planning Studiousguy
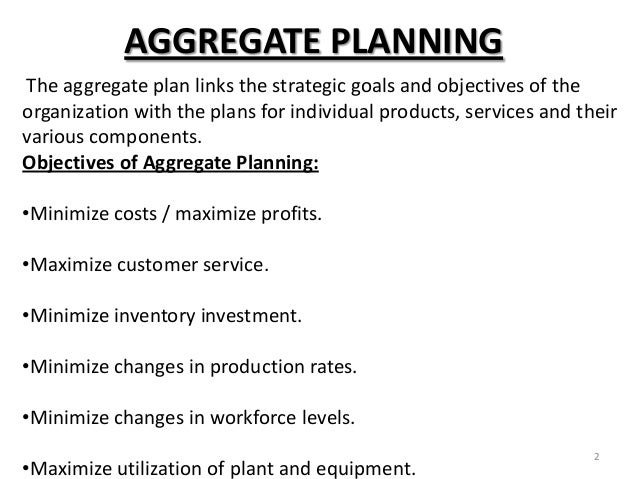



Models Of Aggregate Planning
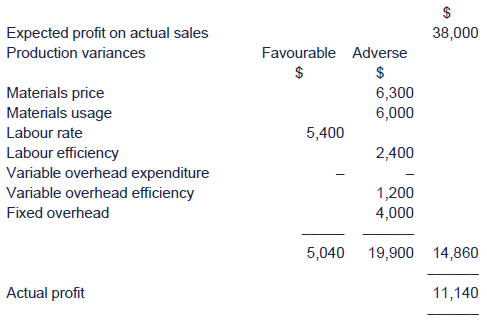



Chapter 17 Questions Answers
0 件のコメント:
コメントを投稿